Quality Assurance vs. Quality Control: What’s the Difference?
While often used interchangeably, Quality Assurance (QA) and Quality Control (QC) play distinct roles in maintaining high standards.
QA is proactive and process-focused, aiming to prevent defects through well-designed systems and procedures. QC, on the other hand, is reactive and product-focused, working to identify and correct defects after they occur. In essence, QA ensures the proper process is followed, while QC ensures the end product meets expectations.
What is Quality Assurance?
Quality Assurance (QA) is a proactive, process-oriented approach to ensuring that quality is built into production or service delivery processes.
QA focuses on preventing defects by systematically improving development and manufacturing processes.
Key characteristics:
- Process-Oriented: QA emphasizes designing and implementing robust processes to prevent defects.
- Preventive: The aim is to detect potential issues early and avoid them altogether.
- Standards-driven: QA relies on frameworks, such as ISO 9001, to define and maintain high-quality standards.
- Documentation: Extensive documentation, such as standard operating procedures and policies, ensures consistency, repeatability, and compliance with industry standards.
Quality Assurance Job Scope
Managing Standard Operating Procedures (SOPs)
QA teams ensure SOPs are easy to understand and follow, are regularly updated, and are uniform across all departments or teams.
Conducting Process Audits
Audits involve evaluating current processes to ensure they meet predefined standards. This includes internal audits conducted by the organization to review its compliance with internal quality management standards, as well as external audits conducted by third-party auditors to validate compliance with regulatory or industry-specific standards.
Employee Training
This includes planning regular training sessions on quality standards, tools, and techniques, and encouraging staff to obtain certifications like Six Sigma or ISO-related training. QA teams are also involved in onboarding programs where they train new hires on quality policies and procedures.
Root Cause Analysis (RCA)
When process failures occur, QA teams perform RCA to identify and eliminate root causes. Common root cause analysis techniques include the “fishbone Diagram” (Ishikawa), which involves visualizing the potential causes of a problem, and the “5 Why analysis,” where the facilitator tries to drill into the issue by asking “Why?” repeatedly with every answer.
Quality Metrics and Reporting
QA teams define and track metrics that provide insights into process effectiveness and efficiency for strategic decision-making. These metrics are industry-specific but can include
- Defect density: The number of defects per unit of output.
- Cycle time: Duration of specific processes.
- Product returns
Risk Management and Mitigation
QA involves continuously evaluating operations for potential quality risks and developing mitigation strategies.
Benchmarking
QA teams compare their organization’s processes and performance against industry leaders or competitors to identify areas for improvement. This benchmarking allows companies to adopt industry best practices, helping them stay competitive.
Continuous Process Improvement
QA fosters a culture of ongoing improvement through frameworks like Kaizen, lean, and Six Sigma
Change Control Management
Quality Assurance (QA) systematically manages changes to processes, equipment, or materials to prevent unintended impacts on quality. They evaluate change requests and conduct impact analyses on those changes.
Supplier Quality Assurance
QA extends beyond internal processes to include the quality of inputs received from suppliers. Activities include:
- Supplier Audits: Ensuring suppliers meet the organization’s quality standards.
- Contract Management: Defining clear quality expectations in agreements.
- Performance Monitoring: Tracking supplier performance over time.
Quality Planning
QA includes planning activities to define quality objectives and align them with organizational goals. This includes setting standards and clarifying responsibilities for maintaining quality.
What is Quality Control?
Quality Control (QC) refers to the reactive, product-oriented aspect of quality management. It focuses on identifying and correcting defects in the final product or service through inspection and testing.
Key characteristics of QC
- Product-Oriented: QC emphasizes evaluating the output to ensure it meets specified quality standards.
- Inspection-Based: QC involves sampling, testing, and measuring to ensure products meet established criteria.
- Focused on Deliverables: QC ensures that the product meets customer expectations and complies with regulatory requirements.
Quality Control Techniques
Sampling:
Sampling involves examining a subset of products from a batch to determine the overall quality of the lot.
- Random Sampling: Selecting items randomly to avoid bias.
- Stratified Sampling: Dividing the batch into groups (strata) and sampling from each.
- Systematic Sampling: Choosing every nth item from a production line.
Once samples have been withdrawn, they are either inspected or tested, depending on the pre-defined procedures and processes.
Inspection
This involves physically examining products, components, or materials to identify defects, non-conformities, or inconsistencies.
Types of Inspection:
- Incoming Inspection: Verifies the quality of raw materials and components supplied by vendors.
- In-Process Inspection: Checks products during production to ensure compliance with standards.
- Final Inspection: Conducted on finished products before delivery to customers.
Testing
Evaluating the performance, durability, or functionality of a product under specific conditions. This aspect of quality control is specific to the industry and product. For example, in the pharmaceutical industry, testing is done to ensure drugs are safe, effective, and meet regulatory standards. It typically involved testing raw materials, in-process products, and finished products using validated and approved testing methods.
Failure testing assesses how and why a product fails under specific conditions, providing insights for improvements.
Statistical Process Control (SPC)
SPC uses statistical methods to monitor and control processes. It helps identify variations in the production process that might lead to defects.
Tools Used in SPC:
- Control Charts: Track process performance over time and highlight deviations from acceptable limits. They consist of three components: the upper control limit, the lower control limit, and the centerline, also known as the process mean.
- Histograms: Show frequency distributions to identify trends or patterns.
Root Cause Analysis (RCA)
Similarly, QC inspectors conduct RCA when product issues arise. For example, when a certain production batch fails to meet quality standards.
Checklists
QC inspectors will use checklists to ensure that all required steps in a process are followed consistently. They provide a simple way to verify compliance. Signed checklists and sampling reports are typically some outputs of QC processes.
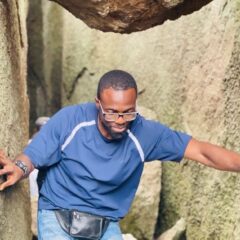
Olutobi
I write about business and project management.
10+ years working in program management. I've worked in health-tech, community health, regulatory affairs and quality assurance.