What Is Six Sigma?
Six Sigma is a data-driven methodology for improving business processes by identifying and eliminating defects, reducing variability, and enhancing quality. It focuses on achieving near-perfect performance using statistical and analytical techniques. Motorola engineer Bill Smith developed Six Sigma in 1986, earning the title “Father of Six Sigma.” The company, led by CEO Bob Galvin, embraced Six Sigma to enhance quality and minimize manufacturing defects. This led to significant product quality and operational efficiency improvements, earning Motorola the Malcolm Baldrige National Quality Award in 1988.
Evolution:
After Motorola’s success, the methodology gained popularity. Companies like General Electric (GE) and Allied Signal adopted and refined it under leaders such as Jack Welch, who made it a core business strategy in the 1990s. Since then, the technique has evolved beyond manufacturing into the healthcare, finance, and IT sectors.
Core Principles
- Focus on customer requirements.
- Use data and statistical analysis to identify root causes of problems.
- Improve processes systematically.
- Reduce variation and defects.
- Foster a culture of continuous improvement.
What does “Six Sigma” mean?
The term comes from statistical process control, where sigma (σ) represents the standard deviation in a process. Achieving “Six Sigma” quality means reducing defects to 3.4 per million opportunities (DPMO), indicating a high level of process performance.
What are the key methodologies of Six Sigma?
The two main methodologies are:
- DMAIC: Define, Measure, Analyze, Improve, and Control (for improving existing processes).
- DMADV: Define, Measure, Analyze, Design, and Verify (for designing new processes or products.
What Do the Six Sigma Belts Mean?
Organizations implementing Six Sigma follow a structured hierarchy with defined roles, similar to martial arts belt levels:
- Yellow Belt: Basic understanding of Six Sigma principles.
- Green Belt: Works on projects and data analysis under the supervision of Black Belts.
- Black Belt: Leads projects, mentors Green Belts, and implements process improvements.
- Master Black Belt: Oversees Six Sigma strategy and trains Black and Green Belts.
- Champion: Senior executive ensuring project alignment with business goals.
How to Get a Six Sigma Certification?
Although no official certification governing body exists, several organisations and institutions offer Six Sigma certifications. While they all adhere to the same fundamental principles, their curricula and certification processes may differ slightly.
American Society for Quality (ASQ)
Website: www.asq.org
International Association for Six Sigma Certification (IASSC)
Website: www.iassc.org
The Council for Six Sigma Certification (CSSC)
Website: www.sixsigmacouncil.org
Since there’s no single governing body, choosing a certification depends on:
- Industry preference (some prefer ASQ, while others accept IASSC).
- The credibility of the issuing organization.
- Whether an accredited course is necessary for your career goals
How much is a Sigma Certification?
Certification prices vary by institution. The pricing details below are gathered from public sources. For current information, please visit the respective websites of these organisations.
1. The Council for Six Sigma Certification (CSSC):
- White Belt: Free
- Yellow Belt: $99
- Green Belt: $159
- Black Belt: $229
- Advanced Certifications: Additional $300 per level
2. American Society for Quality (ASQ):
- Yellow Belt: $394 (non-members), $294 (members)
- Green Belt: $438 (non-members), $338 (members)
- Black Belt: $538 (non-members), $438 (members)
3. International Association for Six Sigma Certification (IASSC):
- Yellow Belt: $195
- Green Belt: $295
- Black Belt: $395
4. Six Sigma Global Institute (SSGI):
- Yellow Belt: $99
- Green Belt: $199
- Black Belt: $299
5. Acuity Institute:
- Lean Six Sigma Green Belt: $499
- Lean Six Sigma Black Belt: $1,795
Is Six Sigma the Same as Lean Six Sigma?
Six Sigma focuses on reducing defects and variation, while Lean focuses on eliminating waste and improving process speed. These two methods are often used together as Lean Six Sigma.
What Is Lean Six Sigma?
Lean Six Sigma combines the principles of Lean (which focuses on reducing waste and improving speed) with Six Sigma’s focus on quality.
The goal is simultaneously improving efficiency, speed, and quality, ensuring optimised and consistent processes.
Key Characteristics:
- Focuses on eliminating waste, reducing non-value-added activities, and improving process flow.
- Leverages tools like 5S, Kaizen, Value Stream Mapping, and Just-In-Time (JIT) along with Six Sigma methodologies.
- It addresses eight types of waste (TIMWOODS): Transportation, Inventory, Motion, Waiting, Overproduction, Overprocessing, Defects, and Skill underutilization.
Can Six Sigma be applied to service industries?
Six Sigma principles can be applied to any industry, including healthcare, finance, and customer service.
How long does it take to complete a Six Sigma certification?
The duration varies by level, but typical timelines are:
- Yellow Belt: A few days
- Green Belt: A few weeks
- Black Belt: Several months
What are the Benefits of Six Sigma?
Implementing Six Sigma can benefit businesses across various industries. Organizations can achieve significant operational and financial advantages by focusing on reducing defects, optimizing processes, and improving overall quality.
1. Improved Quality and Consistency
- It helps businesses achieve higher quality standards by reducing defects and process variations.
- This leads to consistent products and services, enhancing customer trust and brand reputation.
2. Cost Reduction
- It helps reduce operational costs, including waste, rework, and scrap, by identifying and eliminating inefficiencies.
- Lower defect rates mean fewer warranty claims, customer complaints, and returns, leading to cost savings.
3. Increased Efficiency and Productivity
- Ir optimizes workflows by streamlining processes, improving resource utilization, and eliminating unnecessary steps.
- Employees spend less time correcting errors and more time on value-added activities.
4. Data-Driven Decision Making
- It promotes decisions based on statistical analysis and factual data, reducing guesswork and improving problem-solving accuracy.
- Tools like control charts and root cause analysis help businesses make informed strategic decisions.
5. Enhanced Customer Satisfaction
- Businesses can better meet or exceed customer expectations by consistently delivering high-quality products and services.
- Improved quality leads to higher customer loyalty and retention, fostering long-term relationships.
6. Competitive Advantage
- Companies implementing this approach can outperform competitors by offering superior products, optimized processes, and lower costs.
- This leads to stronger market positioning and a better reputation.
7. Better Compliance with Industry Standards
- Many industries (e.g., healthcare, finance, and manufacturing) have strict regulatory and compliance requirements. Six Sigma helps businesses meet these standards by ensuring processes adhere to best practices.
8. Employee Engagement and Development
- It fosters a culture of continuous improvement, empowering employees with problem-solving skills and encouraging teamwork.
- Certification programs provide staff with valuable career development opportunities.
9. Risk Reduction
- Helps identify potential risks in processes.
10. Increased Revenue and Profitability
- Higher quality, reduced waste, and improved efficiency directly increase profitability.
- Companies using Six Sigma often experience substantial improvements in their bottom line over time.
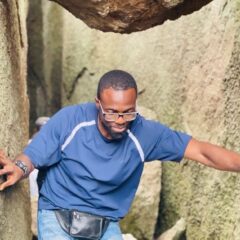
Olutobi
I write about business and project management.
10+ years working in program management. I've worked in health-tech, community health, regulatory affairs and quality assurance.