Corrective Action and Preventive Action (CAPA)
Corrective Action and Preventive Action (CAPA) concept is used in various industries, particularly manufacturing, pharmaceuticals, and quality management, to identify, address, and prevent issues affecting product quality, compliance, and operational efficiency. While both terms are related concepts, they do not have the same meaning.
Corrective Action (CA):
- Taken in response to an existing problem, defect, or nonconformity.
- Aims to eliminate the root cause of an issue to prevent recurrence.
Preventive Action (PA):
- Implemented to identify and mitigate potential risks before they lead to a problem.
- Focuses on proactive measures to prevent nonconformities from occurring.
The CAPA Process
A structured CAPA process typically includes the following steps:
- Problem Identification: Detect issues through customer complaints, audits, inspections, or production data.
- Root Cause Analysis (RCA): Use tools like the 5 Whys or Fishbone Diagram to determine the root cause.
- Develop an Action Plan: Define corrective and/or preventive measures to address the root cause.
- Implementation: Execute corrective or preventive actions, such as process changes, employee training, or equipment upgrades.
- Verification & Effectiveness Check: Monitor the results to ensure the issue is resolved and does not recur.
- Documentation & Compliance: Maintain detailed records for regulatory compliance and continuous improvement.
How CAPA Forms Are Used
A CAPA form is designed to administer the CAPA process. A well-designed CAPA form typically includes the following sections:
1. Basic Information
- CAPA Number: A unique identification code for tracking.
- Date Opened: The date the CAPA was initiated.
- Department: The affected area (e.g., production, quality control).
- Responsible Person(s): Individuals accountable for investigating and implementing actions.
2. Issue Description
- Source of Issue: How the issue was detected (e.g., audit, customer complaint, internal inspection).
- Detailed Description: A clear explanation of the problem, including affected products, processes, or systems.
3. Root Cause Analysis (RCA)
- Investigation Findings: Summary of data, observations, and testing.
- Root Cause Determination: Determining underlying causes using methods like 5 Whys or Fishbone Diagram
4. Corrective Action Plan (CA)
- Immediate Action Taken: Steps to contain or mitigate the issue.
- Corrective Action: Measures to eliminate the root cause and prevent recurrence.
- Implementation Timeline: Target dates for completion.
5. Preventive Action Plan (PA)
- Risk Assessment: Evaluation of potential future occurrences.
- Preventive Measures: Process improvements, training, additional monitoring, or policy updates.
6. Verification & Effectiveness Check
- Follow-up Review: Assessment to confirm that actions were successfully implemented.
- Effectiveness Metrics: KPIs or audits to track recurrence prevention.
7. Closure & Documentation
- Final Approval: Signature of quality assurance or management.
- Date Closed: When the CAPA is officially completed.
Software for Tracking CAPAs
Managing CAPA manually can be inefficient, which is one reason companies are switching to quality management system software. These software solutions help companies document, investigate, assign actions, track progress, and verify effectiveness within a centralized system.
Here are some popular options:
- ETQ Reliance
- MasterControl CAPA Software
- Greenlight Guru (for medical devices)
- TrackWise Digital (for pharma and biotech)
How MasterControl CAPA Works
1. Issue Identification & Initiation
- Users can log a CAPA request through the system (e.g., from an audit, customer complaint, or internal inspection).
- The system assigns a unique CAPA number and timestamps the entry for tracking.
- CAPAs can be linked to deviations, nonconformances (NCs), audits, or complaints for better traceability.
2. Root Cause Analysis (RCA)
- The software provides built-in RCA tools.
- Investigators can attach supporting documents, audit reports, or test results directly within the CAPA record.
- Once the root cause is identified, the system prompts users to define corrective and preventive actions.
3. Action Assignment & Workflow Automation
- The CAPA is assigned to responsible individuals or teams with specific due dates.
- The system automatically sends email notifications and reminders to ensure timely completion.
- Tasks can be tracked via dashboards, allowing managers to monitor progress in real-time.
4. Implementation & Verification
- Users document corrective actions taken, including changes to procedures, equipment, or employee training.
- The system enforces a review and approval workflow, ensuring all actions are verified before closure.
- Effectiveness checks can be scheduled, requiring follow-up audits or quality checks to confirm the issue does not recur.
5. Reporting, Compliance & Audit Readiness
- The software automatically generates reports for CAPA trends, recurring issues, and compliance gaps.
- Reports can be exported for regulatory audits (FDA, ISO, GMP) or internal quality assessments.
- CAPA records are stored in a secured database to maintain regulatory compliance.
Operational Requirements for CAPA in ISO 9001:2015
The operational requirements for CAPAs and CAPA reports under ISO 9001:2015 primarily focus on:
- Corrective Actions (Clause 10.2) – Addressing and eliminating the root cause of nonconformities.
- Risk-Based Thinking (Clause 6.1) – Proactively identifying and preventing potential issues.
Corrective Action Requirements (Clause 10.2)
The standard requires organizations to identify, address, and prevent recurrence of nonconformities by:
(10.2.1.a) Responding to non-conformities
- Taking action to control and correct the issue.
- Addressing the consequences of the nonconformity.
(10.2.1.b) Conducting Root Cause Analysis (RCA)
- Investigating to determine the root cause.
- Assessing whether similar issues exist elsewhere in the organization.
(10.2.1.c) Implementing Corrective Actions
- Defining and executing actions to eliminate the root cause.
- Evaluating the need for additional risk mitigation measures.
(10.2.1.d) Reviewing the Effectiveness of Actions
- Monitoring CAPA implementation to ensure nonconformity does not recur.
(10.2.2) Documentation & Reporting
- CAPA findings, actions, and follow-up must be documented and retained as evidence of continual improvement.
Preventive Action Through Risk-Based Thinking (Clause 6.1)
ISO 9001:2015 replaces formal “Preventive Actions” with Risk-Based Thinking. Organizations must:
- Identify potential risks in processes, products, or services.
- Assess the impact and likelihood of risks.
- Implement preventive measures (e.g., process improvements, audits, training) to reduce risks.
- Monitor effectiveness through continual improvement initiatives.
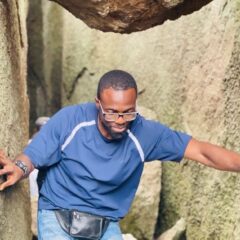
Olutobi
I write about business and project management.
10+ years working in program management. I've worked in health-tech, community health, regulatory affairs and quality assurance.