What Is Kaizen?
Kaizen is a Japanese philosophy centred on continuous improvement. Derived from the Japanese words kai (change) and zen (good), Kaizen translates to “change for the better”. It emphasizes small, incremental changes that collectively lead to significant efficiency, productivity, and quality improvements. Kaizen is not just about running continuous improvement projects. It’s a daily mindset of constant improvement across the organization where everyone finds ways to deliver value more efficiently. At the heart of Kaizen is the belief that improvement is a never-ending process.
According to www.Kaizen.com, Kaizen is underpinned by 5 core principles:
- Know Your Customers.
- Let It Flow
- Go to Gemba
- Empower people
- Be Transparent
Know Your Customers
Understand your customers’ needs, preferences, and pain points. Whether you are conducting interviews or using website analytics, the goal is to listen actively to identify recurring themes and uncover both pain points and opportunities for improvement. It concerns continuous engagement with customers rather than conducting periodic “voice of the customer” projects.
Let It Flow
“Let it Flow” emphasizes the need for a smooth transition from one process to the next without interruptions. When flow is optimized, bottlenecks, delays, and unnecessary waiting times are minimized, leading to faster and more efficient production cycles. Eliminating waste through flow involves streamlining the production process so that resources are used more effectively. For example, Kaizen encourages the integration of just-in-time (JIT) production, where materials are delivered exactly when needed, reducing excess inventory and preventing overproduction.
Muda
Muda is the Japanese word for waste. In production environments, waste refers to any activity or resource that does not add value to the product or service being created. There are seven common types of waste:
Overproduction:
Overproduction occurs when more products are made than are needed or requested by customers. This waste ties up resources and increases the risk of products becoming obsolete, requiring rework, or ultimately being discarded if demand shifts or changes.
Inventory:
Excess inventory, whether raw materials, work-in-progress (WIP), or finished goods, is another form of waste. Storing too much inventory leads to higher storage costs, takes up valuable space, and can result in obsolete stock.
Waiting:
Waiting means there is idle time in the production process, such as employees waiting for materials, tools, or information to continue their work. This can lead to downtime and reduced productivity.
Excess Motion:
Unnecessary movement of workers or equipment. This could involve workers walking long distances to retrieve tools, bending or reaching repeatedly to access materials, or making unnecessary adjustments to machines.
Defects:
Defects refer to products or components that do not meet quality standards and need to be reworked, repaired, or discarded.
Overprocessing:
Overprocessing occurs when more work is done on a product than is necessary to meet customer requirements. This could involve using more complex or expensive processes, tools, or materials than are needed, or adding features that don’t enhance the product’s value.
Unutilized Talent:
Unutilized talent waste happens when employees’ skills, knowledge, and abilities are not fully leveraged. This can occur when workers are not engaged in decision-making processes or are performing tasks that don’t require their full capabilities. It represents a lost opportunity for improvement and innovation, which can reduce overall productivity and employee morale.
Go to Gemba
The term “Gemba” is a Japanese word that translates to “the real place” or “the shop floor,” and it represents the place where value is created. It’s about observing the work processes firsthand, engaging with employees, and gaining an authentic understanding of challenges and opportunities.
The Benefits of Going to Gemba
By visiting the Gemba, leaders and managers can:
- Identify root causes of issues in processes that may not be evident from a distance.
- Understand the workflow and how employees interact with the processes.
- Build relationships with employees by showing genuine interest in their work and challenges.
- Foster a culture of openness and collaboration with shopfront staff.
Gemba walks is the term used for these visits and the expectation is that during Gemba walks, managers do the following:
- Ask questions
- Listen actively to employees to understand their perspectives.
- Observe processes in their natural environment.
- Look for opportunities to improve safety, efficiency, or quality.
- Respect the people performing the tasks.
Empower People
“Empower people” refers to the practice of giving employees the authority, responsibility, and support to contribute to continuous improvement. This means encouraging them to take ownership of their work processes including finding ways of improving them.
these are some recommended tactics to achieve people empowerment:
- Training and Skill Development: Providing employees with the necessary tools and training to make informed decisions and improvements in their areas of work.
- Encouraging Initiative: Creating a culture where employees feel confident to suggest changes, propose innovations, and make improvements without fear of failure.
- Collaboration and Teamwork: Fostering a collaborative environment where employees work together to share ideas, solve problems, and enhance processes.
- Recognition and Support: Celebrating the contributions of employees and acknowledging their role in the continuous improvement process.
- Decentralized Decision-Making: Encouraging decision-making at all levels of the organization, allowing employees to make quick, impactful decisions in their specific areas of expertise.
Be Transparent
“Be Transparent” is about cultivating an open environment where communication, data, feedback, and accountability are not just encouraged but integrated into everyday operations. This transparency builds trust and accelerates problem-solving. Here’s a breakdown of what transparency means in Kaizen:
Clear Communication:
Everyone is informed about goals, processes, performance metrics, and challenges.
Data Sharing:
Sharing data and performance indicators openly allows for collective analysis and decision-making. When data is readily available, employees can identify areas for improvement, and all stakeholders can make informed choices about the best course of action.
Encouraging Feedback:
Employees should feel safe to voice concerns, suggest ideas, and offer constructive criticism. This feedback loop is essential to Kaizen’s continuous improvement model.
Ownership and Accountability:
When processes and results are transparent, individuals take greater ownership of their work. They understand the impact of their actions on the larger system and are more likely to be accountable for their results.
Visibility of Problems and Solutions:
Instead of hiding issues, Kaizen encourages discussing them openly so that solutions can be found collectively, leading to more effective and sustainable improvements.
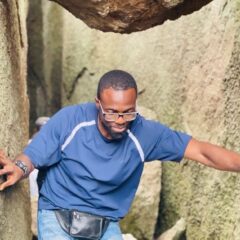
Olutobi
I write about business and project management.
10+ years working in program management. I've worked in health-tech, community health, regulatory affairs and quality assurance.