What Is DMAIC?
DMAIC stands for “Define, Measure, Analyze, Improve, and Control.” It is a systematic, data-driven approach to improving processes and solving problems. DMAIC is primarily used in Six Sigma projects but can also be applied across various industries and disciplines where process improvement is needed.
The Five Phases of DMAIC
- Define
- Measure
- Analyze
- Improve
- Control
Define
The key objective of the define phase is to identify the problem or opportunity for improvement and set clear goals. However, if the issue is not a priority for the organization, you might struggle to get buy-in from stakeholders.
Key Activities:
- Define the scope of the project.
- Identify the stakeholders and customers.
- Create a project charter that outlines the objectives, timelines, and deliverables.
- Develop a high-level process map to understand the current workflow.
Tools Used:
- SIPOC diagram (Suppliers, Inputs, Processes, Outputs, Customers)
- Voice of the Customer (VOC) analysis
- Project charter templates
Outputs:
- A project charter serves as the blueprint for the project.
- A high-level process map, such as a completed SIPOC diagram.
- flowcharts for process visualization.
- Stakeholder Analysis
Measure
The objective of the measure phase is to collect data to establish a baseline for current performance and understand the extent of the problem. This ensures the project is data-driven, objective, and focused on tangible improvements.
Key Activities:
- Identify key performance indicators (KPIs). Common metrics include defects per unit (DPU), cycle time, and process yield.
- Develop data collection plans: Define the data needed to measure process performance, identify data sources, establish data collection methods, and assign responsibilities for data gathering.
- Conduct measurements to determine the process’s baseline performance. Use historical data or directly measure the performance. Also, ensure data is collected consistently and accurately. And that the measurement tools are precise, reliable, and accurate.
Tools Used:
- Statistical Process Control (SPC)
- Process capability analysis
- Data collection sheets and checklists
- Histograms and Control Charts: To visualize data distribution and trends.
Outputs
- SPC Charts and other data visualizations.
Analyze
The Analyze phase is the third step in the DMAIC. This phase is for identifying the root causes of process inefficiencies or defects.
Key Activities
- Conduct Root Cause Analysis (RCA) using techniques like 5 Why analysis or the Fishbone Diagram (Ishikawa) analysis.
- Validate Hypotheses with Data: Using data from the Measure phase to test hypotheses about root causes.
- Map Cause-and-Effect Relationships: Verifying How Process Inputs Influence the Outcome.
- Prioritize Root Causes: Focus on critical factors that have the most significant impact on the problem.
Tools Used:
- Fishbone Diagrams
- 5 Whys Technique
- Hypothesis Testing: To statistically confirm root causes.
Outcome
- Root Cause Identification with supporting evidence
- A refined problem statement based on the insights gained.
Improve
This phase focuses on developing and implementing solutions to address the root causes identified in the Analyze phase. The goal is to optimize the process, reduce variability, and achieve measurable improvements in performance.
Key Activities:
- Brainstorm and develop solutions using brainstorming sessions or creativity techniques like mind mapping
- Evaluate and prioritize solutions using tools like the Impact/Effort Matrix
- Pilot the Solutions.
- Collect data during the pilot phase to assess performance improvements.
Once the pilot results confirm the solution’s effectiveness, the next step is to roll out the improvements across the entire process. You’d need a detailed implementation plan to ensure smooth execution.
Control
The final step in the DMAIC methodology is the Control Phase. Its purpose is to ensure the improvements implemented in the previous phase are sustained. Without proper controls, even the best improvements can deteriorate over time.
Key Activities
- Develop a Monitoring Plan: Establish a monitoring system using tools such as control charts or dashboards.
- Standardize the Process: Create or update standard operating procedures (SOPs) to reflect the improved process.
- Implement Process Control Measures:
- Train Process Owners and Teams
- Conduct audits or reviews to verify that the controls are functioning as intended.
- Monitor and Report: Use control charts, dashboards, or automated alerts to monitor performance in real-time.
Overcoming Challenges with DMAIC Initiatives
Process improvement projects are challenging to pitch due to the widespread perception that they offer minimal economic benefits. There’s generally more attention on production volume and revenue generation, and less so on efficiency. Therefore, it’s essential to emphasize that an effective DMAIC project necessitates disciplined execution. These are some recommendations:
- Start with a well-defined and measurable problem statement in the Define phase. Ensure alignment between the project objectives and organizational goals to prioritize high-impact issues.
- Gain sponsorship and buy-in from top management to secure resources and foster buy-in from the rest of the organization.
- Assign clearly defined roles, such as a project leader and team members, to maintain focus and accountability.
- Base all decisions on accurate, reliable data collected during the Measure phase.
- Pilot and test solutions before full-scale implementation to ensure feasibility and effectiveness.
- Communicate the project’s purpose, progress, and benefits to all stakeholders to gain their support.
- Match tools to the complexity of the problem to avoid overcomplicating simple issues.
- Develop a comprehensive control plan, including SOPs, training, and error-proofing measures.
- Set realistic timelines for each phase to ensure thorough analysis and implementation.
- Conduct a post-project review to evaluate the success of the DMAIC project.
DMAIC provides a systematic approach to process improvement that can lead to significant and sustainable enhancements when executed properly. However, the success of any DMAIC project depends on strong leadership, a data-driven mindset, and thorough planning, with a focus on continuous monitoring and improvement. When applied correctly, DMAIC not only solves problems but also drives operational excellence and long-term success.
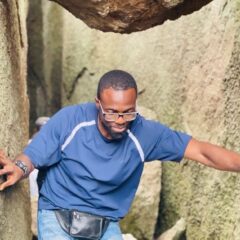
Olutobi
I write about business and project management.
10+ years working in program management. I've worked in health-tech, community health, regulatory affairs and quality assurance.