What Is Quality Planning?
ISO 10005:2018, titled “Quality management — Guidelines for quality plans,” provides comprehensive guidance on creating, reviewing, accepting, applying, and revising quality plans. This standard applies to quality plans for any intended output, whether a process, product, service, project, or contract, and is relevant to organizations of all sizes and sectors.
A quality plan, as defined by ISO 10005, is a document that specifies the quality practices, resources, and sequence of activities pertinent to a particular product, service, project, or contract. It ensures customer requirements and quality objectives are met effectively and efficiently.
ISO 10005:2018 serves as a guide for organizations interested in developing quality plans and can be used regardless of whether they have established a quality management system.
Components of a Quality Plan
The document outlines the following key components for developing a quality plan:
- Scope and Purpose
- Quality Objectives
- Responsibilities and Authorities
- Resource Management
- Process Control
- Documentation Requirements
- Verification and Validation
- Control of Nonconformities
- Continual Improvement
Scope and Purpose
This section outlines the specific boundaries of the quality plan and its objectives. It clarifies what the plan aims to achieve and the areas to which it applies, such as a specific product, service, or project.
Quality Objectives
These are specific, measurable goals that align with customer requirements, regulatory standards, and organizational targets. Objectives provide a clear benchmark for success. They should meet the SMART criteria (Specific, Measurable, Achievable, Relevant, Time-bound). For example, the goal is to achieve a defect rate of less than 1% in manufactured products over the next 12 months.
Responsibilities and Authorities
This section defines the responsibilities for various activities and decisions within the quality management process. It promotes accountability in the overall process.
Here’s an example of how this section is worded:
Quality Assurance (QA) Manager: Oversees the development and implementation of the quality plan.
Line Supervisor: Ensures workers follow approved procedures during production.
It may also be used to clarify who has the authority to make decisions about quality-related issues, such as approving changes, accepting deviations, or halting production. Or to identify backup responsibilities or authorities in case of unexpected changes, such as staff turnover or emergencies.
Resource Management
This addresses the identification, allocation, and effective utilization of resources required to achieve quality objectives. Different resource types have their considerations.
Personnel Resources
Key considerations include:
- Required skills and competencies for each role.
- Training or certifications to meet quality objectives.
- Methods for evaluating personnel qualifications (e.g., competency assessments or audits).
Equipment and Tools
- Specifications for required equipment.
- Maintenance and calibration schedules.
- Have backup equipment or contingency plans in place in case of equipment failure.
Material Resources
- Quality specifications for materials.
- Procedures for inspecting and approving incoming materials.
- Inventory management practices to ensure adequate supplies without waste.
Financial Resources
- Estimated costs for personnel training, equipment acquisition, maintenance, and inspections.
- Processes for monitoring budget adherence and addressing cost overruns.
Facilities
- Layout and design considerations for efficiency and compliance
- Maintenance and cleanliness of facilities to support quality.
Process Control
Establishes detailed methods for managing, monitoring, and controlling processes to ensure consistent quality. This may include sampling, testing, and measuring to ensure products meet established criteria, or setting control limits around processes, such as using statistical process control (SPC) to monitor the consistency of a production line.
Documentation Requirements.
Specifies the documentation required to support the quality plan, including standard operating procedures, work instructions, and records. For example, a manufacturing company may require detailed inspection records for each batch of products. It should also cover documentation storage and retrieval processes.
Verification and Validation
Describes how outputs are checked to confirm they meet quality requirements. This includes product testing or examination. For example, in pharmaceutical manufacturing, chemical analysis is conducted on sampled batches before the batches are released for distribution. Product batches are kept in post-production quarantine until the quality analysis results.
Control of Non-conformities
Defines the procedures for identifying, documenting, and addressing outputs that do not conform to requirements. For example, the quality plan might specify immediate quarantine and rework procedures for such products. Different organizations employ various techniques for analyzing root causes, including the 5-why analysis and fishbone analysis. CAPA (Corrective and Preventive Action) forms are used to identify the root cause of an issue, implement corrective actions, and prevent similar issues from happening again.
Continual Improvement
Includes mechanisms to collect feedback, measure performance, and implement improvements in the quality plan.For example, support ticket analysis – using customer complaints to identify areas of improvement.,
The Plan-Do-Check-Act (PDCA) cycle, also known as the Deming Cycle, is a continuous improvement framework used to enhance processes and solve problems systematically. It begins with the Plan phase, where objectives are set, and strategies are developed based on identifying areas for improvement. The Do phase implements the planned actions on a small scale to test their effectiveness. During the Check phase, results are evaluated against the expected outcomes, identifying successes and areas for adjustment. Finally, in the Act phase, successful changes are standardized and implemented broadly, or the cycle is repeated with refinements.
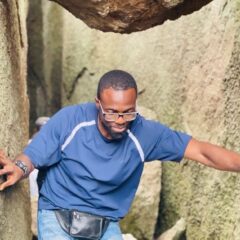
Olutobi
I write about business and project management.
10+ years working in program management. I've worked in health-tech, community health, regulatory affairs and quality assurance.