Lean management has gained popularity as a highly efficient approach for improving productivity and reducing organisational waste. From the manufacturing sector, lean principles have expanded to various industries, offering valuable insights on maximizing resources, streamlining operations, and consistently delivering high-quality products or services.
The Five Core Principles of Lean Management
Lean management is founded on five guiding principles, each aimed at fostering continuous improvement.
These core principles are:
- Define Value
- Mapping the Value Stream
- Create Flow
- Implement a Pull System
- Pursue Perfection
Let’s look at each principle and practical ways of applying them.
Define Value
Find out what value means to your customers. A valuable output is any product or service that customers will pay for, but work that does not contribute to that output is waste. To understand customer needs and expectations, conduct surveys, interviews, or customer journey analyses. Then, develop a clear value proposition based on the information collected.
Value Stream Mapping
Create a visual map of the entire production process, highlighting value-adding and non-value-adding steps (waste). Include people from various departments involved in the process to ensure a holistic view. Value Stream Maps consist of four main components, starting with the customer. These components are:
- Customer
- Processes
- Suppliers
- Communication Processes
Value Stream Map Symbols
Various symbols are used in Value Stream Mapping. For example;
Process Box (Rectangle): Represents each step in the process, typically showing a single activity or task. A small rectangle below each process box contains key data such as cycle time, wait time, and inventory levels.
Inventory Triangle: Denotes points where inventory is stored, such as raw materials, work-in-progress (WIP), or finished goods. it contains the amount of inventory in units.
Kaizen Burst (Star Symbol): Highlights areas that require immediate improvement or are undergoing Kaizen (continuous improvement) activities.
Value Stream Map Data
Various data can be collected to create a value stream map. The data you collect will depend on the specific project and objectives. Generally, these data will assist in understanding how efficient your production cycle is:
Lead Time: The total time from the moment a request is made until the product or service is delivered to the customer. It includes all stages of the process, including waiting, delays, and any non-value-added activities.
Cycle Time: Cycle Time (C/T) is the time required to complete one unit or a single task from start to finish within a specific process step. It only considers the actual time spent actively working on the task and excludes waiting or downtime between steps.
Value-added time (VAT) is the amount of time in a process that directly contributes to creating value in the final product or service.
Wait Times: The time products or services spend waiting between different process steps.
Rework Time: Time taken to fix defects.
Non-Value Adding Time: Time spent on non-value-adding (non-production) activities such as meetings, and training sessions.
How to Draw a Value Stream Map
- Define the Process: Choose a specific process to map (e.g., order fulfilment, production workflow). Set clear boundaries: start and endpoints.
- Gather Information: Collect data on each step, including time, inventory, and resources used.
- Draw Basic Workflow: Use symbols to represent key elements: processes, inventory, and flow. Arrange steps in sequential order, from left to right.
- Add Flow Lines: Use arrows to show the flow of materials and information through each step.
- Include Metrics: Add relevant metrics, such as process time, lead time, and cycle time for each step.
- Identify Waste and Bottlenecks: Look for delays, excess inventory, or unnecessary steps to improve efficiency.
- Create a Future State Map: Once you’ve mapped the current state, sketch a future state map that eliminates waste and optimizes flow.
Create Flow
After management eliminates wasteful procedures, they can proceed to the next principle of lean management, which focuses on creating an efficient workflow.
Tactics for Improving Operational Flow.
- Balance Workload: Redistribute tasks or add resources to balance work across steps. This ensures no single stage becomes overloaded.
- Simplify Tasks: Break down complex steps or simplify tasks that often slow down the process.
- Create SOPs (Standard Operating Procedures): Develop clear instructions for each step to ensure everyone follows a uniform approach, reducing variations and errors.
- Use Checklists, visual cues, and reminders.
- Cross-Train Employees: Cross-training enables flexibility, allowing staff to step in and keep the flow moving if bottlenecks or resource gaps arise.
- Smaller batches: Instead of processing large batches, consider working on items individually or in smaller batches.
- Optimize Workstation Layout: Position workstations, tools, and materials in a way that minimizes movement and transport time.
- Use Visual Management Tools: Kanban boards, whiteboards, or Project management software tools that display the status of each stage.
- Hold Daily Stand-Up Meetings: A brief daily meeting keeps teams aligned and allows them to address potential blockers, fostering a collaborative approach to maintaining flow.
- Implement Quality Checks: Conduct quality checks at each stage rather than waiting until the end. This prevents defects from accumulating across the production line.
Implement a Pull System
Move from a “push” to a “pull” system by producing only when there is customer demand. This contrasts with the traditional “push” system, where items are produced in anticipation of demand and then “pushed” to customers.
Key Elements of a Pull System
- Customer Demand Drives Production: Workflows and production are initiated by actual customer orders, not by predictions or estimated demand.
- Reduced Waste: Since production is closely aligned with customer demand, the pull system avoids the waste associated with overproduction, excess inventory, and unnecessary storage.
- Kanban as a Visual Control: Kanban cards signal when more inventory or parts are needed, helping to manage inventory levels without overproduction
The entire production process is structured so that each step only begins once the previous step is completed. However, when demand is highly variable or unpredictable, a pull system can be challenging to implement without stockouts or delays. Therefore, hybrid approaches might be necessary. It is also important to establish reliable supplier relationships to ensure they can meet demand quickly.
Pursue Perfection
Continuously seek improvement in all aspects of the business. Encourage a culture of innovation and adaptability. Hold regular Kaizen meetings to identify improvement opportunities. Collect employee feedback to refine processes and reduce errors over time.
Adopting lean principles can boost efficiency, reduce waste, and enhance customer satisfaction. By analyzing processes, streamlining workflows, and fostering continuous improvement, businesses can build a flexible framework that keeps them competitive in changing markets.
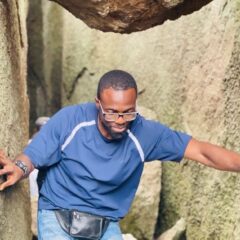
Olutobi
I write about business and project management.
10+ years working in program management. I've worked in health-tech, community health, regulatory affairs and quality assurance.