Receiving goods from vendors is not a passive task—it’s a critical control point that can affect everything from production schedules to customer satisfaction. Here’s why having a formal SOP for receiving orders is essential:
Ensures Product Quality and Compliance
An SOP standardizes inspections and quality checks. This helps prevent substandard, counterfeit, or contaminated materials from entering the production line, which is crucial in regulated industries like food, pharmaceuticals, and electronics.
Minimizes Operational Risk
Without a structured process, warehouses risk accepting wrong or damaged items, which can lead to delays, rework, or production stoppages. A defined SOP mitigates these risks by clearly outlining roles, responsibilities, and required checks.
Improves Traceability and Accountability
SOPs require documentation at every step—delivery, inspection, approval, or rejection—creating a reliable paper trail. This is critical for internal audits, regulatory compliance, and resolving supplier disputes.
Supports Vendor Performance Monitoring
By documenting non-conformances and delivery inconsistencies, the receiving process becomes a feedback loop for supplier management. This data is essential for evaluating vendor reliability and negotiating future contracts.
Streamlines Training and Onboarding
Following a documented SOP can help new warehouse staff quickly learn the correct procedures. This reduces dependency on informal knowledge and increases process consistency across shifts and teams.
Sample SOP: Receiving Orders from Vendors
Purpose
This SOP standardises the process of receiving vendor shipments, ensuring quality, accuracy, and compliance with manufacturing standards. It outlines how to verify, document, and safely integrate incoming goods into the facility’s inventory or quarantine processes.
Scope This SOP applies to all incoming materials—raw materials, components, packaging supplies, and equipment—delivered by external vendors to the manufacturing facility.
Responsibility
- Warehouse Staff: Initial receiving, inspection, documentation
- Quality Control (QC): Quality inspection and quarantine clearance
- Procurement: Vendor coordination and purchase order (PO) validation
- Inventory Team: Stock updating and location assignment
Procedure
1. Pre-Arrival Coordination
- Ensure all Purchase Orders (POs) are recorded and accessible.
- Notify the warehouse team of expected delivery dates and contents.
- Prepare designated receiving and quarantine areas.
2. Initial Receiving and Documentation
- Inspect the delivery vehicle upon arrival for signs of tampering or damage.
- Cross-reference delivery documents with the PO and Bill of Lading.
- Check for:
- Correct product
- Correct quantity
- Correct batch or serial numbers
- Condition of packaging
Note: Any discrepancies must be reported immediately to procurement and logged in the Non-Conformance Report (NCR) system.
3. Quarantine and Segregation
- Do not release received goods directly into inventory or production.
- Move all incoming materials to a clearly labeled quarantine area.
- Tag with a “Hold” status pending quality control.
4. Quality Control Inspection
- QC inspects for compliance with specifications (dimensions, certifications, expiry dates, etc.).
- Conduct sampling or lab testing if applicable (especially for raw materials or perishables).
- Approve, reject, or request corrective action based on results.
5. System Updates and Approval
- Update the ERP or inventory management system with:
- Inspection results
- Approval/rejection status
- Storage location assignment
- Approve items for movement into designated storage or production use.
6. Rejection and Return Process
- Isolate rejected items and label clearly to prevent accidental use.
- Notify vendor with documented evidence of non-conformance.
- Initiate return, rework, or disposal process based on vendor agreement.
7. Post-Receiving Reporting
- Document the entire receiving process for traceability:
- Delivery time/date
- Inspection results
- QC personnel involved
- NCR references (if any)
Risk Management Considerations
- Contamination or Mix-ups: Prevent by enforcing quarantine protocols and labeling.
- Counterfeit or Substandard Goods: Implement vendor vetting and serial number tracking.
- Inventory Errors: Use barcode/RFID scanning to minimize manual entry.
- Delayed Production: Build buffer time into the production schedule to accommodate inspection delays.
Supporting Documents and Records
- Purchase Orders
- Bill of Lading
- Quality Inspection Checklist
- Non-Conformance Report (NCR)
- Vendor Communication Logs
- Inventory Update Logs
This document will include a section for references and any changes made to the history.
In addition, you can cover the following FAQs during your SOP training.
Frequently Asked Questions (FAQs)
1. Why is it necessary to quarantine items after receiving them?
Quarantine ensures that no unverified or non-compliant goods enter production or inventory. It allows the QC team to inspect materials for quality, safety, and specification compliance. Skipping this step increases the risk of product recalls, production downtime, or regulatory violations.
2. What should I do if the shipment is missing documentation?
Immediately log the issue and notify Procurement. Do not proceed with receiving or inspection until all essential documents—like the delivery note, PO, or Certificate of Analysis (if required)—are provided. This protects the facility from legal and traceability issues.
3. Can I accept partial deliveries?
Yes, but it must be clearly documented. Update the inventory system to reflect what was received, tag it as a partial delivery, and inform procurement for follow-up. Be sure to inspect and quarantine even the partial shipment.
4. What are the most common mistakes during the receiving process?
Some common errors include:
- Skipping documentation checks
- Failing to quarantine materials
- Accepting damaged or incorrect items
- Mislabeling received goods
- Neglecting to notify procurement or QC of discrepancies
5. What if the vendor is a trusted, long-term supplier—do we still need to inspect the goods?
Yes. Even reliable vendors can experience batch errors, packaging issues, or logistical mishaps. QC inspections are not about distrust; they are a necessary part of quality assurance and traceability.
6. Who is responsible for rejected items?
The warehouse team is responsible for isolating and tagging the items. Procurement coordinates with the vendor for return, replacement, or credit. QC provides the formal justification for rejection, usually via a Non-Conformance Report.
7. What’s the best way to store approved items after inspection?
Once cleared, items should be:
- Moved to the correct storage area (e.g., cold storage, raw materials zone, secure cage)
- Labeled with item name, batch number, and date received
- Logged into the inventory system with storage location details. This ensures accurate stock levels and easy traceability.
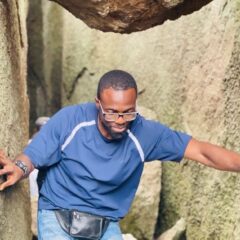
Olutobi
I write about business and project management.
10+ years working in program management. I've worked in health-tech, community health, regulatory affairs and quality assurance.