Getting Ready
Preparing for a Good Manufacturing Practice (GMP) audit requires a structured approach to ensure compliance with regulatory requirements and industry best practices. Here’s a step-by-step guide to help you prepare:
1. Understand the Scope
- Determine the type of audit and who the auditors are. i.e. internal, external, or regulatory (e.g., FDA, EMA, WHO).
- Identify the specific GMP standards applicable to your facility
- Review previous audit findings to address any recurring issues.
2. Assemble a Preparation Team
- Assign roles and responsibilities to key personnel from Quality Assurance (QA), Manufacturing, Engineering, and other departments.
- Designate a point of contact to coordinate the audit process and communicate with auditors.
- Conduct a pre-audit meeting to align expectations.
3. Conduct a Gap Analysis
- Perform an internal audit to identify non-conformities before the official audit.
- Use a GMP compliance checklist to ensure all areas meet regulatory standards.
- Document findings and implement corrective actions.
4. Review Documentation and Records
- Ensure Standard Operating Procedures (SOPs) are up to date and reflect current practices.
- Verify batch records, deviation reports, training records, validation documents, and CAPAs (Corrective and Preventive Actions).
- Organize logbooks and maintenance records for easy retrieval.
5. Train Employees
- Conduct GMP refresher training for all staff to reinforce compliance.
- Practice mock interviews to ensure employees confidently answer auditor questions.
6. Prepare the Facility
- Perform a walkthrough inspection of your facility.
- Identify potential issues that may be flagged or prompt further investigation into your operations.
7. Develop an Audit-Day Strategy
- Assign a designated escort to guide auditors through the facility.
- Set up a document review area where auditors can inspect records comfortably.
- Encourage employees to provide concise and factual responses without volunteering unnecessary information.
What Happens on Audit Day?
Here’s a breakdown of what typically happens on the GMP audit day:
1. Opening Meeting
- The audit begins with an introductory meeting between auditors and key facility personnel (e.g., Quality Assurance, Manufacturing, Regulatory Affairs).
- The auditor explains the scope, objectives, and methodology of the audit.
- The facility may give an overview presentation about its operations and quality systems.
2. Facility Walkthrough (Plant Tour)
- Auditors inspect production areas, warehouses, laboratories, and other key sites.
- They observe cleanliness, organization, and adherence to SOPs (Standard Operating Procedures).
- Equipment and facility conditions, such as maintenance records and calibration status, are examined.
- Auditors may check for potential cross-contamination risks, pest control measures, and employee hygiene compliance.
3. Documentation Review
Auditors examine records to ensure compliance with GMP standards. Key documents include:
- Batch manufacturing records (BMRs) – Ensure consistency in production.
- Standard Operating Procedures (SOPs) – Must be approved, followed, and periodically reviewed.
- Training records – Verify employees are trained on GMP and job-specific procedures.
- Quality control and lab records – Check analytical test results, raw material approvals, and release procedures.
- Change control, deviations, and CAPAs (Corrective and Preventive Actions) – Ensure non-conformities are documented and addressed.
4. Employee Interviews
- Auditors may question employees about their roles and responsibilities.
- They assess whether staff understands GMP principles, follows SOPs, and can explain their work processes clearly.
- Auditors may randomly select employees to discuss how they handle deviations, record-keeping, and hygiene procedures.
5. Data Integrity and Traceability Checks
- Auditors scrutinize electronic and paper records for inconsistencies, alterations, or missing data.
- They verify audit trails, timestamps, and compliance with ALCOA+ principles (E.g., Attribution, Legitimacy, Contemporaneity, Originality, and Accuracy).
- Traceability is tested by tracking raw materials to finished products (e.g., lot number tracking, supplier verification).
6. Review of Compliance to Regulatory Guidelines
- Auditors compare the company’s processes with GMP regulations (e.g., FDA 21 CFR Part 211, EU GMP, WHO GMP).
- They assess the firm’s quality culture, including how management ensures compliance and continuous improvement.
7. Closing Meeting & Audit Findings Presentation
- Auditors summarize observations, deficiencies, and compliance strengths.
- They classify findings into categories such as:
- Critical – Major violations posing health risks or regulatory action.
- Major – Significant non-conformities requiring prompt correction.
- Minor – Issues needing improvement but not immediate risks.
- If any findings are noted, the facility may be required to submit a Corrective and Preventive Action (CAPA) plan within a set timeframe.
Tactics for a Successful Audit
- Be ready at All Times
- Organize Documentation for Easy Access
- Train and Empower Employees
- Conduct a Pre-Audit Walkthrough
- Assign a document retrieval team to provide records quickly.
- Have subject matter experts (SMEs) available to answer auditor-specific questions.
- Manage Auditor Interactions Professionally
- Ensure records comply with ALCOA+ principles (Attributable, Legible, Contemporaneous, Original, Accurate, and more).
- Keep audit trails intact for electronic and manual records.
- If an auditor identifies an issue, acknowledge it professionally and explain your action plan.
- Avoid arguing or being defensive—show commitment to continuous improvement.
- Conduct a Strong Closing Meeting, recapping findings and action items.
- If non-conformities are found, outline your corrective action plan and expected timelines.
- Follow Up and Implement Corrective Actions
-
- Address audit findings promptly and document corrective actions.
- If required, submit a CAPA (Corrective and Preventive Action) report within the auditor’s deadline.
- Monitor compliance improvements through ongoing internal audits and reviews.
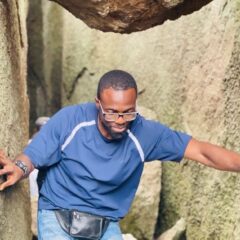
Olutobi
I write about business and project management.
10+ years working in program management. I've worked in health-tech, community health, regulatory affairs and quality assurance.