What Is Operations Management?
Operations management (OM) is the backbone of any organization. It ensures that business processes run efficiently, optimize resources, and meet customer expectations. OM involves planning, organizing, and overseeing production and service delivery to maximize efficiency and effectiveness.
It bridges the gap between strategy and execution, ensuring business goals align with operational activities.
Key Functions
Process Design and Improvement
A well-structured process leads to higher efficiency, lower costs, and better quality. Operations managers develop, analyze, and refine workflows to eliminate bottlenecks, minimize waste, and improve productivity. Popular methodologies include:
-
- Lean Management: Focuses on reducing waste and improving efficiency.
- Six Sigma: Uses data-driven techniques to minimize defects and improve quality.
- Total Quality Management (TQM): Encourages a company-wide commitment to quality improvement.
Supply Chain Management
Coordinating the flow of materials, products, and information across suppliers, manufacturers, and customers is crucial for meeting demand while minimizing costs.
This involves:
Capacity Planning
Operations managers forecast demand and determine the necessary resources—workforce, machinery, and facilities—to meet production and service needs.
Inventory Management
Effective inventory control ensures that the right materials and products are available at the right time, preventing stockouts and overstocking.
Key strategies include:
-
- Economic Order Quantity (EOQ) to optimize order sizes.
- ABC Analysis to prioritize inventory management based on value.
- Automated Inventory Systems that track stock levels in real-time.
Quality Control
Maintaining high production and service delivery standards enhances customer satisfaction and reduces defects. Techniques like Statistical Process Control (SPC) help monitor quality.
Quality control methods include:
-
- Statistical Process Control (SPC) to monitor production quality.
- ISO Certification to standardize quality practices.
- Kaizen (Continuous Improvement) to refine operations regularly
Technology and Automation
Integrating digital tools, AI, and automation streamlines operations, reduces costs and improves precision in manufacturing and service industries.
-
- Artificial Intelligence (AI): Automates decision-making and predictive analytics.
- Internet of Things (IoT): Enhances real-time monitoring of operations.
- Robotic Process Automation (RPA): Reduces manual work in administrative tasks.
Importance of Operations Management
- Enhances Efficiency: Streamlined processes reduce costs and improve output.
- Improves Customer Satisfaction: Efficient operations ensure timely delivery and high-quality products/services.
- Drives Competitive Advantage: Companies that optimize operations can reduce costs and innovate faster.
- Supports Sustainability: Sustainable operations minimize waste and reduce environmental impact.
Operations management principles apply across various industries but with unique applications:
- Manufacturing: Focuses on production planning, quality control, and supply chain efficiency.
- Retail: Involves inventory management, logistics, and customer experience optimization.
- Healthcare: Manages hospital workflows, patient care, and resource allocation.
- Technology & Software: Ensures seamless product development, cloud operations, and cybersecurity.
- Service Industry: Improves customer service processes, staffing, and operational efficiency.
Each industry has specific challenges and operational strategies tailored to its needs.
Operations Management and Asset Management
Operations management and asset management are closely linked. Both focus on optimizing resources to improve efficiency, reduce costs, and maximize the value of a company’s assets. While operations management oversees daily business functions and workflows, asset management ensures that physical and intangible assets are effectively utilized, maintained, and optimized to support operations.
For example, in production,
Operations managers work to keep production or service delivery running smoothly with minimal interruptions. Asset managers implement preventive maintenance strategies to extend the lifespan of assets and reduce unplanned downtime.
In some organizations, a senior ops. manager or chief operating officer may supervise asset and/or fleet management.
Career Path
An operations manager typically progresses through various roles, gaining experience in different aspects of operations before moving into senior leadership. Here’s a common career trajectory:
1. Entry-Level Roles (0-3 Years)
- Ops. Analyst: Assists in process analysis, data collection, and reporting.
- Logistics Coordinator: Manages supply chain operations and inventory control.
- Production Supervisor: Oversees a team in manufacturing or service operations.
2. Mid-Level Roles (3-7 Years)
- Operations Supervisor: Manages daily workflows and team performance.
- Supply Chain Manager: Oversees procurement, logistics, and vendor relations.
- Project Manager (Operations): Leads process improvement initiatives.
3. Senior-Level Roles (7-15 Years)
- Operations Manager: Takes responsibility for end-to-end business operations.
- Plant Manager (Manufacturing): Manages factory operations, production, and quality.
- Director of Operations: Leads operational strategy and oversees multiple teams.
4. Executive-Level Roles (15+ Years)
- Vice President (VP) of Operations: Shapes company-wide operations strategy.
- Chief Operating Officer (COO): Oversees the entire business’s operational structure.
- CEO (in some cases): Some COOs transition into CEO roles, especially in operations-driven industries.
Key Skills Required
- Strong analytical and problem-solving skills.
- Knowledge of operations methodologies (Lean, Six Sigma, Kaizen, etc.).
- Financial acumen for budgeting and cost control.
- Leadership and team management abilities.
- Proficiency in supply chain and logistics management.
- Data-driven decision-making and strategic thinking.
How to Advance in Operations Management
- Gain Cross-Functional Experience: Work in different areas like supply chain, quality control, and finance.
- Earn Certifications: Lean Six Sigma, PMP (Project Management Professional), and APICS CPIM (Certified in Production and Inventory Management) add credibility.
- Develop Leadership Skills: Strong communication, negotiation, and team management abilities are crucial for career growth.
- Stay Updated with Industry Trends: Embrace automation, AI, and sustainability practices.
- Pursue Advanced Education: An MBA in Operations or Supply Chain Management can open doors to senior roles.
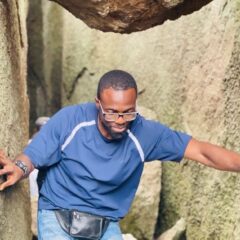
Olutobi
I write about business and project management.
10+ years working in program management. I've worked in health-tech, community health, regulatory affairs and quality assurance.