What Is Process Improvement?
Process improvement refers to the practice of analyzing and refining business processes to achieve greater efficiency, effectiveness, and adaptability. It involves identifying inefficiencies, redundancies, or bottlenecks in existing workflows and implementing changes to enhance performance.
At its core, process improvement aims to deliver value by:
– Reducing costs and waste.
– Improving customer satisfaction.
– Increasing employee productivity and morale.
– Enhancing agility in response to market demands.
Why Process Improvement Matters
Organizations that prioritize process improvement gain several competitive advantages:
- Cost Savings: By eliminating non-value-adding activities, companies reduce operational expenses.
- Consistency and Quality: Streamlined processes lead to standardized outcomes, minimizing errors and improving quality.
- Employee Satisfaction: Efficient processes reduce frustration, freeing employees to focus on high-value tasks.
- Customer Delight: Faster and more reliable service translates to better customer experiences.
Key Methodologies for Process Improvement
Lean Management
Lean focuses on maximizing value while minimizing waste. Rooted in the manufacturing industry, Lean principles apply to various sectors, emphasizing the removal of inefficiencies and streamlining workflows. Tools such as value stream mapping and the 5S framework (Sort, Set in Order, Shine, Standardize, Sustain) are commonly used.
These are the five principles of lean management:
- Define Value: Find out what value means to your customers. A valuable output is any product or service that customers will pay for, but work that does not contribute to that output is waste.
- Map the Value Stream: Develop a visual map of the entire production process, highlighting value-adding and non-value-adding steps (waste).
- Create Flow: Create an efficient workflow using various tactics like having SOPs, balancing workload and cross-training employees.
- Implement a Pull System: Producing only when there is customer demand.
- Pursue Perfection: Continuously seek improvement in all aspects of the business
Six Sigma
Six Sigma aims to improve process quality by identifying and removing defects. It leverages either of these approaches to achieve its goals:
- DMAIC: Stands for Define, Measure, Analyze, Improve, and Control.
- DMADV: Stands for Define, Measure, Analyze, Design, and Verify.
Kaizen
Kaizen is a Japanese philosophy centred on continuous improvement. Derived from the Japanese words kai (change) and zen (good), Kaizen translates to “change for the better”. It emphasizes small, incremental changes that collectively lead to significant efficiency, productivity, and quality improvements. Kaizen is not just about running continuous improvement projects. It’s a daily mindset of constant improvement across the organization where everyone finds ways to deliver value more efficiently. At the heart of Kaizen is the belief that improvement is a never-ending process. It has 5 core principles:
- Know Your Customers. Understand your customers’ needs, preferences, and pain points.
- Let It Flow. Ensure a smooth transition from one process to the next.
- Go to Gemba: It’s about observing the work processes firsthand,
- Empower people: Giving employees the authority, responsibility, and support to contribute to continuous improvement.
- Be Transparent: Cultivating an open environment where data, feedback, and accountability are integrated into everyday operations
PDCA Cycle
The PDCA cycle is a four-step iterative process in which each phase builds on the previous one, ensuring data-informed decisions and sustainable outcomes. Developed by Dr. W. Edwards Deming and rooted in quality management principles, the PDCA technique equips organizations with a practical framework for continuous improvement.
The steps in PDCA are:
- Plan: Involves identifying the problem or improvement opportunity, defining project objectives and designing potential solutions with a focus on feasibility.
- Do: Here, the focus shifts to implementation. That is, execute the plan on a small scale to minimize risks.
- Check: Comparing actual outcomes with expected results.
- Act: Implementing successful strategies on a larger scale, or making adjustments as a new cycle starts
Overcoming Challenges in Process Improvement
Continuous improvement is essential for organizations striving for long-term success, but it is not without challenges. Here are some common obstacles businesses face when embedding a culture of continuous improvement:
Resistance to Change
Employees may be hesitant to adopt new processes or abandon familiar workflows for fear of job displacement, increased workload, or scepticism about the effectiveness of changes.
Solution: Foster open communication, involve employees in decision-making, and highlight the benefits of continuous improvement.
Lack of Leadership Commitment
Without strong buy-in from leadership, process improvement initiatives often lack direction, resources, and prioritization.
The solution is to educate leadership on the benefits of process improvement and to align initiatives with the organization’s strategic objectives.
Insufficient Resources
Limited time, budget, or personnel can hinder the successful implementation of process improvement projects. Organizations that undervalue process improvement also don’t adequately budget for such projects.
Solution: Advocate for process improvement to be a part integral part of operations, having KPIs like any other aspect. That way, securing the necessary budget will be easier.
Poor Communication
Miscommunication about goals, expectations, or changes can create confusion and reduce engagement. The solution is to establish clear communication channels, provide regular updates, and ensure transparency about progress and setbacks.
Lack of a Structured Approach
Without a clear framework or methodology, process improvement efforts can become disorganized and ineffective.
The key is to understand the different methodologies and know how to apply them to different scenarios.
Employee Fatigue
Continuous improvement can lead to “change fatigue” if employees feel overwhelmed by constant adjustments. So, pace changes appropriately and celebrate milestones
Silos and Lack of Collaboration
Departments operating in silos may resist sharing information or working together to implement improvements. Beyond competing priorities, having the right organizational culture is important. Organizations should focus on building trust first, before jumping on improvement projects.
Unrealistic Expectations
Expecting immediate or overly ambitious results from process improvement projects can lead to disappointment. So, it’s important to set the right expectations. Continuous improvement is not a one-time project.
Over-Reliance on Tools
Focusing on tools and software for continuous improvement instead of understanding the core principles and applications. The solution is to improve the quality and frequency of training for continuous improvement professionals
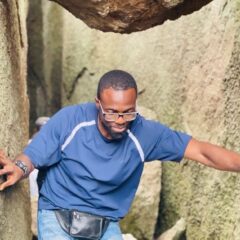
Olutobi
I write about business and project management.
10+ years working in program management. I've worked in health-tech, community health, regulatory affairs and quality assurance.