Efficient inventory management ensures businesses maintain the right stock levels, reduce costs, and meet customer demands. In this article, we’ll explore various inventory management techniques, their advantages and disadvantages, and how to choose the best fit for your business.
Just-in-Time (JIT)
This technique involves aligning production and procurement processes with customer orders. JIT is an inventory strategy where goods are ordered and received only as they are needed. A manufacturing company using JIT orders raw materials based on actual production schedules. For instance, an automotive company might receive parts only hours before assembly. This minimizes waste and storage costs. It also reduces the risks of overstocking finished products. It is best suited for businesses with predictable demand and reliable suppliers. However, this technique can leave businesses vulnerable to supply chain disruptions.
ABC Analysis
ABC analysis is an inventory management technique that assigns a value to each item based on its importance to the business. The ranking is based on critical data such as demand, cost and revenue. Inventory managers then group items into classes based on these criteria. These classes are then used to determine which items should be stocked and in what quantities.
For example,
Class A could be high value, high demand, high revenue volume
B, moderate value, demand and revenue.
C, Low value, demand and revenue.
ABC analysis prioritizes critical stock items and Improves resource allocation. However, classifying items is time-intensive and requires constant updates. It is best for retailers, wholesalers, or manufacturers managing diverse inventories.
Economic Order Quantity (EOQ)
The economic order quantity (EOQ) calculates the ideal order quantity to minimize total inventory costs. It has the formula:
EOQ = √ [2DS/H]
D = Demand in units (annual)
S = Order cost
H = Holding costs (per unit, per year)
Demand in units is derived from historical demand data.
Holding cost is calculated by adding all the costs associated with storing your inventory and then dividing that total by the total value of your inventory.
Order cost includes all expenses incurred in purchasing and receiving inventory items.
One significant drawback of the Economic Order Quantity (EOQ) calculation is its reliance on stable input data. There may be seasonal fluctuations in customer demand or swift changes in economic factors that influence order costs but which will affect the EOQ calculation.
First-In-First-Out (FIFO)
First-In-First-Out means the oldest stock is sold first. Common with perishable goods and products prone to expiry. Businesses aiming to adopt and maintain a First-In-First-Out (FIFO) inventory management system must ensure that their storage practices align with this technique. This can be achieved by placing new inventory behind the older stock, which helps create a natural FIFO flow. Additionally, it is important to label product boxes clearly with information about their purchase or production dates, making it easy to identify older stock quickly. Furthermore, educating warehouse or store staff about FIFO and its significance in reducing waste is crucial.
Perpetual Inventory System
This system utilizes real-time tracking software to monitor inventory levels, meaning that inventory is automatically updated after each transaction. Unlike periodic inventory systems, which depend on manual stock counts at set intervals, the perpetual system uses technology to maintain continuous records of stock changes resulting from sales, purchases, or returns. A point-of-sale (POS) system or barcode scanner records each activity.
While this approach reduces errors associated with manual inventory counts, it does require investment in hardware (such as scanners) and software. Additionally, the system can be susceptible to various technical challenges, including human error, knowledge gaps, and system outages. Even with a perpetual system in place, it is essential to perform physical counts occasionally to verify the accuracy of the data.
Vendor-Managed Inventory (VMI)
This arrangement transfers the responsibilities of stock level monitoring, replenishment planning, and inventory restocking from the buyer to the vendor. This shift ensures optimal stock availability while reducing the operational burdens on the buyer. A replenishment agreement or similar contract governs this arrangement including minimum and maximum inventory levels, replenishment timelines, and performance KPIs.
The buyer provides the vendor with access to inventory levels, sales data, and forecasted demand, allowing the vendor to ship the necessary stock to maintain the agreed inventory levels. However, poor vendor performance or reliability issues can lead to disruptions in the supply chain.
Batch Tracking
Batch tracking is an inventory management technique that monitors and records the movement of goods based on specific batches or lots. A batch is a group of items produced or purchased together, sharing the same production date, expiration date, or other identifying details. This method is commonly used to ensure product quality, traceability, and compliance in industries like manufacturing, food production, and pharmaceuticals. As products move through the supply chain—from production to storage to sale—the system records where each batch is at any given time. If an issue arises, businesses can quickly trace affected batches for targeted recalls or quality inspections. Many industries, like food and pharmaceuticals, require batch tracking for regulatory compliance.
GS1 standards are globally recognized systems for identifying, capturing, and sharing product information through unique identifiers. These standards play a critical role in enhancing batch tracking by providing a unified framework for identifying and tracing products across the supply chain. GS1 assigns Global Trade Item Numbers (GTINs) to products, enabling seamless data sharing across different systems and supply chain partners.
Dropshipping
Dropshipping is a retail fulfilment method in which a store does not hold its own inventory. Instead, when a customer places an order, the retailer purchases the item from a third-party supplier who then ships it directly to the customer. In this setup, the retailer acts as an intermediary, managing sales and customer service, while the supplier takes care of inventory and shipping. The retailer profits by charging the customer a higher price than the wholesale price paid to the supplier. Since there is no need to invest in inventory or warehousing, dropshipping is accessible for new entrepreneurs. However, retailers have limited control over inventory, packaging, or the quality of shipping.
Safety Stock Management
Safety stock management entails maintaining a buffer of extra inventory to avoid stockouts caused by unpredictable demand, supply chain disruptions, or other uncertainties. This extra stock serves as a cushion, ensuring that businesses can continue operations and meet customer demand, even when inventory levels are lower than expected. It strikes a balance between the cost of holding additional inventory and the potential loss of sales due to stockouts.
There’s a more complex calculation for safety stock, but here’s a simpler approach:
Safety Stock=(Maximum daily usage×Maximum lead time)−(Average daily usage×Average lead time)
The main drawback is that it locks up funds that could be used for other investments.
Choosing the Right Inventory Management Technique
Business Size
Small Businesses: Techniques like periodic inventory systems or ABC analysis may suffice for small businesses due to lower inventory volumes and simpler requirements. Larger operations may need advanced methods such as perpetual inventory systems or Just-in-Time (JIT) to handle complexity and scale.
Industry Type
Retail: Techniques like First-In-First-Out (FIFO) are critical for managing perishables or products with short shelf lives.
Healthcare: GS1 Standards and batch tracking ensure compliance and traceability for sensitive products like medicines.
Product Type
Perishable Goods: Methods like FIFO manage shelf life effectively.
High-Value Items: Economic Order Quantity (EOQ) or ABC analysis prioritizes inventory control for high-cost products.
Customized Goods: Techniques like JIT align inventory with production schedules to minimize waste.
Demand Variability
Stable Demand: Methods like EOQ are ideal for consistent, predictable sales patterns.
Fluctuating Demand: Techniques such as Safety Stock Management or Demand Forecasting ensure availability during demand surges or drops.
Available Technology
Low-Tech Businesses: Periodic inventory methods or manual ABC analysis can work for businesses with minimal technological support.
Tech-Savvy Businesses: Perpetual systems, RFID tracking, or cloud-based inventory software enhance real-time visibility and control.
Business Goals
Cost Minimization: Techniques like JIT or EOQ** reduce holding and ordering costs.
Stockout Prevention: Safety stock management and demand forecasting help prevent stockouts and ensure timely delivery.
Storage Capacity
Limited Space: JIT minimizes stored inventory.
In conclusion, various inventory management techniques each have their benefits and drawbacks. The choice of one or more techniques depends on the type of business, industry, and other relevant factors.
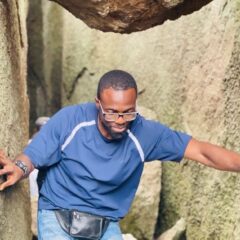
Olutobi
I write about business and project management.
10+ years working in program management. I've worked in health-tech, community health, regulatory affairs and quality assurance.