What is the 5S Methodology?
The 5S methodology is a workplace organization system designed to enhance efficiency, reduce waste, and improve productivity. It originated in Japan and is widely used in Lean manufacturing and other continuous improvement practices. The name comes from five Japanese words representing each step in the process:
- Seiri (Sort)
- Seiton (Set in Order)
- Seiso (Shine)
- Seiketsu (Standardize)
- Shitsuke (Sustain)
Seiri (Sort)
- Identify what is essential and what is not.
- Remove clutter and redundant tools, materials, or equipment.
- Use a “red tag” system to mark and review items for disposal or relocation.
A typical red tag includes the following details:
- Description: A brief description of the item (e.g., “Old printer”).
- Reason for Tagging: Why the item is tagged (e.g., “Not in use”).
- Owner/Department: Who owns or is responsible for the item?
- Action Required: What needs to be done (e.g., “Discard,” “Relocate”).
- Date: When the item was tagged.
- Deadline: A deadline for deciding what to do with the item.
Seiton (Set in Order)
- Arrange tools, equipment, and materials in a logical order.
- Assign a specific location for each item.
- Visual cues like labels, shadow boards, or floor markings are used to streamline retrieval.
Seiso (Shine)
- Perform regular cleaning and maintenance of tools and equipment.
- Identify and address root causes of dirt or disorder (e.g., spills, leaks).
- Encourage employees to take ownership of keeping their workstations clean.
Seiketsu (Standardize)
- Develop clear, documented procedures and schedules for sorting, organizing, and cleaning.
- Use visual management tools (e.g., checklists, charts).
- Train employees to follow standardized practices.
Shitsuke (Sustain)
- Foster a culture of discipline and continuous improvement.
- Conduct regular audits to ensure adherence to 5S practices.
- Recognize and reward teams for maintaining standards.
5S Method in Practice
The 5S method is applicable in various industries and settings. Companies frequently employ it to address challenges such as disorganisation, time wastage, workflow inefficiencies, and safety hazards caused by clutter. These problems can diminish productivity, raise operational expenses, and lead to employee dissatisfaction.
Office Workspace Organization
Problem: A cluttered office with piles of documents, misplaced supplies, and inefficient filing systems.
Sort (Seiri)
- Identify unnecessary items (e.g., old files, unused office supplies, broken equipment).
- Dispose of outdated documents or digitize them.
- Use a “red tag” system to temporarily set aside items you’re unsure about and decide later.
Set in Order (Seiton)
- Assign a specific place for frequently used items, such as pens, staplers, or notebooks.
- Implement a filing system for documents (e.g., color-coded folders).
- Label drawers, cabinets, and storage bins for quick identification.
Shine (Seiso)
- Clean desks, monitors, keyboards, and shared office equipment regularly.
- Create a weekly cleaning schedule for shared spaces like the break or meeting rooms.
Standardize (Seiketsu)
- Develop a shared guide for organizing desks and files.
- Use digital tools for reminders (e.g., calendar alerts for cleaning days).
Sustain (Shitsuke)
- Encourage employees to tidy their desks at the end of each day.
- Hold monthly reviews to ensure compliance and discuss improvements.
Healthcare Facility Maintenance
Problem: A clinic or hospital with scattered medical supplies and hygiene challenges.
Sort (Seiri)
- Remove expired medications and medical supplies.
- Separate essential equipment from rarely used items and store them in a designated area.
Set in Order (Seiton)
- Use labelled containers for different medical supplies.
- Use colour-coded bins for waste segregation (e.g., biohazard, recyclable).
- Arrange items in the order they are used during procedures.
- Install shelving with clear labels for easy restocking.
Shine (Seiso)
- Sanitize work surfaces, patient rooms, and equipment daily.
- Create a log for tracking cleaning schedules.
Standardize (Seiketsu)
- Develop protocols for cleaning and organizing after each shift.
5. Sustain (Shitsuke)
- Train staff regularly on 5S principles.
- Monitor compliance (via continuous quality assurance practices) and provide feedback during team meetings.
Digital Work Space Optimization
Problem: A cluttered digital workspace characterised by:
- Difficulty Finding FIles: Employees waste considerable time searching for documents due to disorganised folder structures or outdated files cluttering shared drives.
- Duplication and Version Confusion: Multiple copies of the same file exist across different locations, leading to confusion over which version is the most up-to-date and creating inefficiencies in collaboration.
Applying the 5S methodology to a digital workspace like Google Workspace or SharePoint can significantly enhance productivity, streamline collaboration, and reduce digital clutter.
Sort (Seiri)
- Audit shared drives or folders for outdated, duplicate, or unused files.
- Remove or archive old documents that are no longer relevant but may be needed for compliance.
- Review permissions and remove access for users who no longer need it.
Set in Order (Seiton)
- Establish a consistent folder hierarchy (e.g., organized by department, project, or year).
- Rename files and folders with clear, standardized naming conventions (e.g., “ProjectName_Team_MeetingNotes_2025-01-01”).
- Pin frequently accessed files or folders in Google Drive or SharePoint for quicker retrieval.
- Use metadata tagging in SharePoint for better searchability and categorization.
- Create shortcuts to essential files or tools in shared folders for team-wide access.
Shine (Seiso)
- Schedule a monthly or quarterly “clean-up day” for teams to review and tidy up shared drives.
Standardize (Seiketsu)
- Create a digital workspace policy document outlining naming conventions, file organization rules, and user roles.
- Use templates for frequently created documents like reports, meeting agendas, or proposals.
- Automate workflows in SharePoint or Google Workspace using tools like Power Automate or Google Apps Script for repetitive tasks.
- Maintain a central repository for policies, training materials, and team-specific resources.
Sustain (Shitsuke)
- Conduct quarterly audits to ensure adherence to digital organization standards.
- Train employees on best practices for managing digital files and collaborating effectively.
- Use dashboards or KPIs to track progress in reducing clutter or improving retrieval times.
- Recognize and reward teams or individuals who consistently follow 5S principles.
Benefits of Applying 5S in Digital Workspaces
- Improved Collaboration: Organized files and standardized practices make it easier for teams to work together.
- Reduced Search Time: Clear naming conventions and logical structures simplify file retrieval.
- Enhanced Security: Regular audits ensure only authorized users have access.
- Optimal Storage: Reduced clutter optimizes storage usage and minimizes costs.
- Scalable Practices: Standardized workflows are easier to replicate across teams or departments.
Like any change initiative or intervention, careful planning is essential to minimize resistance. To gain support, begin by outlining the benefits—such as reduced stress, enhanced efficiency, and improved teamwork. Involve employees in the process by encouraging them to share ideas for organising their workspace. Concentrate on small, visible successes during the initial stages to build momentum and provide training and resources to facilitate a smoother transition.
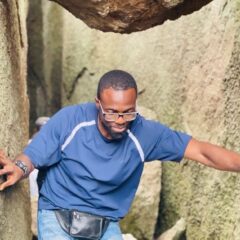
Olutobi
I write about business and project management.
10+ years working in program management. I've worked in health-tech, community health, regulatory affairs and quality assurance.