The Rise of Sustainable Operations
In today’s business landscape, sustainability is no longer a fringe concept—it’s a competitive imperative. As companies face mounting pressure from consumers, regulators, and investors to reduce their environmental footprint, many are rethinking how products are designed, manufactured, and delivered. Enter the zero-waste supply chain, a transformative approach to operations that aims to eliminate waste at every stage of the supply cycle.
But what exactly does a zero waste supply chain involve? How is it different from general green supply chain practices? And most importantly, how can organisations begin adopting this model to drive environmental and economic value?
This article explains the concept, benefits, challenges, and implementation strategies for building a zero-waste supply chain in 2025 and beyond.
What Is a Zero Waste Supply Chain?
A zero-waste supply chain is designed and managed to prevent waste from being generated at any point in the process, from raw material sourcing and manufacturing to packaging, distribution, and product end-of-life. The ultimate goal is to ensure that all resources are reused, recycled, or composted rather than sent to landfills or incinerated.
This model draws heavily from circular economy principles, where materials flow in closed loops rather than linear “take-make-dispose” systems.
Key Characteristics:
- Design for reuse or recyclability
- Sustainable sourcing of raw materials
- Waste-minimising manufacturing processes
- Reverse logistics for used or expired products
- Supplier partnerships focused on circular practices
- Data-driven waste auditing and optimisation
Why Zero Waste Matters for Supply Chains
Transitioning to a zero-waste model isn’t just about corporate responsibility—it has tangible business benefits. Companies that invest in waste reduction can realise cost savings and brand loyalty while future-proofing their operations against evolving regulations.
1. Environmental Impact
Reducing waste means fewer raw materials are extracted and less pollution is generated. This leads to:
- Lower greenhouse gas emissions
- Less landfill contribution
- Reduced water and energy usage
2. Financial Efficiency
Zero waste practices often improve operational efficiency by reducing overproduction, streamlining inventory, and reusing materials. Companies save money on:
- Waste disposal fees
- Procurement of virgin materials
- Energy costs through leaner operations
3. Brand Reputation and Customer Trust
Sustainability-conscious consumers are more likely to support brands that are transparent about their environmental practices. Such a commitment can:
- Differentiate your brand in crowded markets
- Increase customer loyalty
- Enhance ESG (Environmental, Social, Governance) scores
How Is Zero Waste Different from Traditional Supply Chain Sustainability?
Many organisations already engage in sustainability practices like using eco-friendly packaging or optimising transport routes. However, zero waste goes a step further by:
- Treating waste elimination as a primary design goal, not an afterthought
- Focusing on systemic change, not isolated green initiatives
- Integrating end-of-life planning into product design and delivery
Think of it this way: if traditional sustainability is like recycling a plastic bottle, this is about not producing the bottle in the first place—or designing it to be infinitely reusable.
Steps to Build a Zero Waste Supply Chain
Transitioning to this model requires coordinated effort across multiple functions—procurement, production, logistics, marketing, and beyond. Here are seven key steps to get started:
1. Conduct a Waste Audit
Start by identifying where waste is generated across your supply chain. Use data analytics and supplier input to map waste hotspots in:
- Raw materials and inputs
- Packaging
- Manufacturing processes
- Product returns and recalls
2. Redesign Products and Packaging
Work with product designers and engineers to eliminate non-recyclable or excessive materials. Strategies include:
- Modular design for easy disassembly
- Biodegradable or compostable materials
- Standardised, refillable containers
3. Choose Circular Suppliers
Partner with vendors and manufacturers who share common goals. Criteria for selection may include:
- Closed-loop material systems
- Take-back programs for packaging
- Environmental certifications (e.g., ISO 14001)
4. Integrate Reverse Logistics
Set up infrastructure for collecting used or end-of-life products. This might involve:
- In-store drop-off points
- Postal return options
- Incentive programs for customer participation
Reverse logistics ensures materials are recaptured and reintegrated into production, rather than discarded.
5. Digitise and Monitor Waste Flows
Leverage digital supply chain tools to track waste metrics, flag inefficiencies, and forecast demand more accurately. Useful technologies include:
- IoT sensors on production lines
- AI-based inventory optimisation
- Blockchain for material traceability
6. Educate Teams and Stakeholders
A zero waste strategy can only succeed if all participants are aligned. Provide ongoing training for:
- Operations and logistics staff
- Procurement officers
- Supplier partners
Cultivate a strong mindset across the organisation.
7. Report and Improve
Set clear KPIs and report progress transparently. Common zero waste supply chain metrics include:
- Waste diversion rate (% not sent to landfill)
- The reuse rate of packaging
- Carbon emissions avoided
- Cost savings from waste reduction
Use these insights to drive continuous improvement.
Real-World Examples of Zero Waste Supply Chains
Interface Inc.
Interface, a global flooring manufacturer, has pioneered zero waste manufacturing through its “Climate Take Back” initiative. The company:
- Uses 100% recycled or bio-based materials
- Has reduced waste to landfill by over 90%
- Operates closed-loop recycling for its carpet tiles
Unilever
Unilever’s factories across multiple countries now send zero non-hazardous waste to landfills. The company achieves this through:
- Advanced waste segregation
- Industrial symbiosis partnerships
- Local community engagement in recycling programs
Challenges to Achieving a Zero Waste Supply Chain
While the benefits are compelling, businesses often face several hurdles in going zero waste:
- Upfront costs of redesigning products or updating infrastructure
- Supplier limitations in sourcing closed-loop materials
- Complex logistics for reverse flows and recycling coordination
- Cultural resistance within teams unfamiliar with circular models
However, these challenges can be overcome with strategic planning, phased implementation, and executive support.
Future of Zero Waste Supply Chains
The convergence of sustainability, technology, and policy makes this approach feasible and increasingly essential.
Emerging trends include:
- AI for predictive waste analytics
- Extended producer responsibility (EPR) regulations
- Product-as-a-service models that eliminate ownership waste
- Collaborative waste marketplaces for industrial byproducts
As governments tighten environmental standards and customers demand greater transparency, companies that lead in zero waste practices will gain a durable edge.
Conclusion: Zero Waste Is a Business Imperative
Zero waste supply chains are no longer a “nice-to-have” for environmentally conscious brands—they are a strategic necessity in an era of finite resources and climate urgency. Businesses that adopt this model can enhance their operational efficiency, strengthen stakeholder trust, and position themselves for long-term success.
Whether you’re a manufacturer, retailer, or logistics provider, the time to start your zero waste journey is now.
Suggested External Links
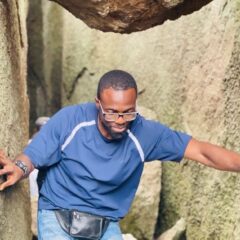
Olutobi
I write about business and project management.
10+ years working in program management. I've worked in health-tech, community health, regulatory affairs and quality assurance.