Well-documented processes help ensure efficiency, consistency, and compliance in any organization. Two of the most common types of process documentation are Standard Operating Procedures (SOPs) and Work Instructions (WIs). However, many professionals struggle with when to use one versus the other and how to manage both effectively.
This article explores the differences between SOPs and Work Instructions, when to use each, and best management practices.
SOPs Versus Work Instructions
SOPs and Work Instructions serve to document processes, but they differ in scope and level of detail.
Scope:
-
An SOP covers multiple tasks within a process, often involving different roles and departments.
-
A WI focuses on a single task, detailing exactly how to complete it.
Level of Detail:
-
SOPs contain general guidelines on the various tasks in a process.
-
WIs are usually action-oriented and provide precise steps for execution.
SOPs can include step-by-step instructions like Work Instructions (WIs), but the main difference is their scope and length. WIs offer detailed, task-level guidance and are usually shorter and more straightforward.
When to Write an SOP vs. a Work Instruction
Understanding when to use each document helps maintain clarity and efficiency in process management.
When to Write an SOP
Write an SOP when:
-
You need to establish a standardized process across teams or departments.
-
The process involves multiple interdependent tasks or steps.
-
Employees need a general understanding of a workflow without getting into detailed steps.
When to Write a Work Instruction
Write a Work Instruction when:
-
A task is complex and requires precise steps to complete.
-
There is a need to reduce errors in task execution.
-
The task is repeated frequently and must be performed consistently.
-
Employees need visual guidance (e.g., screenshots, diagrams).
-
The process involves specialized equipment or software that requires specific handling.
Examples of Work Instructions:
-
How to process a refund in an ERP system
-
How to operate a CNC machine
-
How to assemble a product
-
How to configure a router for network security
In some cases, it makes sense to keep them together or to have either one, such as in short, self-contained processes.
Managing SOPs and Work Instructions Together
Since both documents serve different but complementary purposes, they must be managed efficiently to avoid confusion and duplication. Here’s how:
1. Establish a Clear Documentation Hierarchy
A structured hierarchy helps differentiate the role of each document:
-
Policies – High-level company rules and regulations.
-
SOPs – Departmental or cross-functional processes.
-
Work Instructions – Detailed guidance for executing specific tasks.
For example, a “Warehouse Management SOP” may include multiple Work Instructions, such as:
-
“How to Receive Incoming Shipments”
-
“How to Store Perishable Goods”
-
“How to Conduct an Inventory Audit”
2. Use a Consistent Format for Both Documents
Standardizing formats improves readability and usability. Consider including:
-
For SOPs:
-
Title and document number
-
Purpose and scope
-
Roles and responsibilities
-
Step-by-step process overview
-
Compliance and references
-
-
For Work Instructions:
-
Task title and document number
-
Tools and materials required
-
Step-by-step instructions
-
Visual aids (images, screenshots, diagrams)
-
Troubleshooting tips
-
3. Store and Maintain Documents in a Centralized System
Use a document management system (DMS) or knowledge base to:
-
Ensure easy access for employees
-
Maintain version control
-
Track updates and revisions
-
Enable search functionality
Popular platforms include SharePoint, Google Drive, Confluence, or specialized SOP software like SweetProcess or Trainual.
4. Review and Update Documents Regularly
Both SOPs and Work Instructions should be living documents that evolve with process changes. Set a review cycle (e.g., every 6-12 months) to:
-
Remove outdated steps
-
Address employee feedback
-
Align with regulatory changes
5. Train Employees on Proper Use
Even the best documentation is useless if employees don’t know how to use it. Provide training and onboarding on:
-
The difference between SOPs and Work Instructions
-
Where to find relevant documents
-
How to follow instructions accurately
6. Link SOPs and Work Instructions for Seamless Navigation
Ensure employees can quickly move between SOPs and Work Instructions as needed. For instance:
-
An SOP for “Product Quality Control” should include links to WIs such as “How to Perform a Quality Inspection”.
-
An SOP for “IT Security Management” should reference WIs like “How to Reset a Password Securely”.
Common Mistakes in Writing SOPs and Work Instructions
-
Being too vague or too detailed: Both documents should provide enough direction without overwhelming the reader.
-
Not involving the right stakeholders – Employees who perform the task should help create such documents
-
Failing to update documents regularly – Processes evolve, and outdated documentation can cause inefficiencies and errors.
-
Poor accessibility – If SOPs and WIs are hard to find, employees won’t use them.
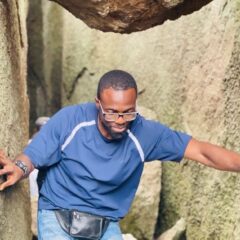
Olutobi
I write about business and project management.
10+ years working in program management. I've worked in health-tech, community health, regulatory affairs and quality assurance.