Warehouse Management Systems (WMS)
A Warehouse Management System (WMS) is software designed to optimize warehouse operations. It provides visibility into inventory levels, tracks inventory movement, and streamlines picking, packing, and shipping processes. It is critical in supply chain management, ensuring efficiency and accuracy in handling goods within a warehouse.
Key Functions of WMS
- Inventory Management: Monitors current inventory levels and oversees stock management across different locations.
- Order Fulfillment: Optimizes picking, packing, and order accuracy.
- Receiving and Putaway: Streamlines receiving and assigns storage for incoming goods.
- Shipping Management: Manages shipping schedules and carriers and automates labels and documentation.
- Reporting and Analytics: Offers insights into warehouse performance and identifies process bottlenecks.
- Labour Management: Tracks employee productivity.
Examples of WMS Software
1. Standalone WMS
Dedicated software focusing exclusively on warehouse operations. For example, HighJump and Manhattan Associates WMS.
2. Cloud-Based
Hosted on the cloud, providing scalability and accessibility. Examples are Oracle Netsuite WMS and SAP Extended Warehouse Management.
3. Integrated WMS with ERP Systems
Combines WMS functionalities with broader enterprise resource planning (ERP) systems. Examples are Microsoft Dynamics 365 and Infor CloudSuite.
4. Open-Source
Cost-effective solutions with customizable features. Examples include Odoo WMS and OpenWMS.org.
5. AI-Driven WMS
Incorporates artificial intelligence for predictive analytics and process automation. Examples include Softeon WMS and Blue Yonder.
Although Shopify isn’t a WMS, it offers built-in tools to track and manage inventory across sales channels. These tools focus on simplicity and real-time synchronization, so small businesses can still use this cost-effective alternative:
- Stock Setup: Merchants input their product quantities and assign stock to locations.
- Sales Synchronization: When a customer places an order, Shopify reduces stock levels in real-time.
- Inventory Replenishment: Merchants manually or automatically reorder stock when levels fall below a predefined point.
- Cross-Channel Updates: Inventory levels are synced across all Shopify-connected channels to prevent overselling.
Setting Up a Warehouse Management System
Setting up a warehouse management system requires careful planning to align with your operational needs. Consider the following key points:
Define Your Business Objectives
- Key Questions:
- What problems are you trying to solve?
- Are you focusing on efficiency, accuracy, scalability, or cost reduction?
- Actionable Step: Clearly document your goals, such as reducing picking errors, increasing inventory visibility, or optimizing labour.
Evaluate Your Current Processes
- Conduct a Workflow Analysis:
- Map your warehouse processes (receiving, putaway, picking, packing, and shipping).
- Identify inefficiencies or bottlenecks that the WMS should address.
- Understand Limitations: Assess the gaps in your current system or manual operations to set benchmarks for improvement.
Define Functional Requirements
- Core Functionalities:
- Inventory tracking (e.g., RFID, barcode scanning).
- Real-time data visibility.
- Integration with other systems (e.g., ERP, TMS, or e-commerce platforms).
- Scalability: Ensure the WMS can grow with your business through additional features or handling higher volumes.
Budget and Cost Considerations
- Direct Costs:
- Software licensing or subscription fees.
- Hardware costs (scanners, printers, servers, etc.).
- Indirect Costs: Implementation, training, and ongoing maintenance.
Vendor Selection
- Evaluate Multiple Vendors: Compare functionality, reputation, customer support, and pricing.
- Request a Demo: Ensure the software meets your requirements in a live demonstration.
- References and Case Studies: Look for success stories in your industry to validate vendor expertise.
Integration with Existing Systems
- ERP Integration: Make sure that the chosen software is compatible with other software your company uses for operations.
User Training and Change Management
- Training Programs: Provide comprehensive training to warehouse staff and managers.
- Change Leadership:
- Communicate the benefits of the WMS to minimize resistance.
- Assign a project champion to oversee adoption.
Warehouse Layout and Technology Alignment
- Adapt Your Layout: Ensure that the physical warehouse setup complements the workflows enabled by the WMS.
- Technology Setup:
- Install necessary hardware (e.g., RFID scanners and handheld devices).
- Implement internet infrastructure for seamless connectivity.
Data Migration and Cleanup
- Inventory Accuracy: Audit and clean existing inventory data to ensure accurate system initialization.
Testing and Piloting
- Test the System: Use a sandbox environment to simulate operations.
- Pilot in a Controlled Environment: Roll out the system in one warehouse or section before full deployment.
Scalability and Customization
- Scalability: Ensure the WMS can handle increased volumes and future needs like multiple warehouse support.
- Customization: Opt for software that allows process-specific customizations without extensive coding.
Regulatory and Security Compliance
- Data Security:
- Ensure compliance with data protection regulations (e.g., GDPR, CCPA).
- Implement user roles and access control.
- Regulatory Compliance: Adhere to industry-specific standards (e.g., FDA regulations for medical devices).
Sample Workflow Using WMS
- A customer places an order through an e-commerce platform, ERP system, or point-of-sale (POS) software.
- The order is automatically synced with the WMS, triggering the picking and fulfilment process.
- The WMS generates a picking list.
- Warehouse staff uses handheld scanners or mobile devices to follow the picking list. Each item is scanned to verify accuracy and update the WMS in real-time, reducing the available inventory count.
- As items are picked, the WMS communicates with the accounting software to adjust inventory on the balance sheet.
- The picked items are moved to a packing station. The packing process is logged, and the WMS verifies that all order items are present.
- The WMS generates shipping labels and updates the order status to “shipped.”
- The cost of goods sold (COGS) is calculated and recorded in the accounting system.
- Once the order is shipped, the WMS triggers the accounting software to generate an invoice, delivery note, and/or receipt.
- The accounting software records the sale.
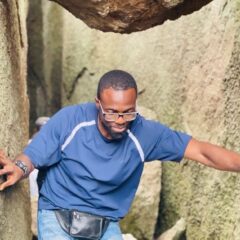
Olutobi
I write about business and project management.
10+ years working in program management. I've worked in health-tech, community health, regulatory affairs and quality assurance.