Supply chain risk management (SCRM) is the process of identifying, assessing, and mitigating risks that could disrupt the flow of goods, services, and information. Effective SCRM ensures business continuity, protects revenue, and enhances operational resilience.
Natural Disasters & Pandemics
Natural disasters present a significant risk to supply chains, as they can disrupt every aspect of the supply process, from raw material procurement to final product delivery. During the COVID-19 pandemic, companies like Toyota had to halt production due to semiconductor shortages.
Natural disasters can devastate transportation routes like roads, railways, and ports, making it challenging or impossible to transport goods. They can also affect workers, rendering them unavailable due to injuries and evacuations. Mitigating tactics include the following:
Diversification
One of the most effective ways to reduce risk is by diversifying suppliers and transportation routes. This can ensure that if one supply line is disrupted, others can take over.
Inventory Buffering
Maintaining a buffer stock of essential materials and goods, especially for critical products, can help mitigate short-term disruptions caused by natural disasters.
Supplier Financial Instability
Suppliers may face financial difficulties that hinder their operations and ability to fulfill contracts, potentially leading to production delays and supply chain disruptions. Companies can mitigate this risk by regularly assessing suppliers’ financial health, diversifying their supplier base, and creating contingency plans.
Supplier Financial Health Assessments
For publicly traded suppliers, companies can review their suppliers’ financial statements (income statements, balance sheets, or cash flow reports) or monitor stock performance. On the other hand, they can use any of these strategies when working with private suppliers:
- Requesting audited financial statements or profit & loss statements.
- Monitoring for workforce reductions, production slowdowns, or management changes.
- Asking other businesses about their experience with the supplier.
Using Supplier Agreements
Companies may include any of the following clauses in their supplier agreements:
Early Termination Clauses
Allows the company to terminate the contract if the supplier faces bankruptcy, insolvency, or financial distress. For example, they may include a clause stating that the contract can be terminated if a supplier fails to meet delivery obligations for three consecutive transactions.
Financial Monitoring & Reporting Requirements
Requires suppliers to provide regular financial statements, audit reports, or credit ratings to assess their financial health. For example, a contract may mandate quarterly financial disclosures to detect early signs of distress.
Alternative Supplier Clauses
This allows the company to quickly switch to an alternative supplier if the primary supplier cannot meet obligations. For example, if a supplier defaults, the company can activate pre-negotiated agreements with a backup supplier without legal complications.
Geopolitical and Trade Risks
These risks arise from political instability, trade policies, tariffs, sanctions, or diplomatic conflicts that disrupt global supply chains. They can lead to higher costs, delayed shipments, restricted market access, or forced relocation of production. US-Canada and U.S.-China trade tensions have resulted in supply-chain uncertainties and additional costs to businesses in both countries. Similarly, Brexit caused supply chain uncertainty for businesses operating in the UK and EU.
Tactics for mitigating geo-political risks include the following:
Geographical Diversification
Sourcing and manufacturing in multiple regions to reduce dependency on one country.
Flexible Sourcing & Dual Suppliers
Maintaining alternative suppliers in different trade zones to pivot quickly when policies change.
Trade Agreements & Policy Monitoring
Staying updated on new regulations, tariffs, and trade policies to adapt early.
Reshoring & Nearshoring
Bringing production closer to home markets to reduce reliance on high-risk regions.
Transportation & Logistics Disruptions
Delays or disruptions can happen due to factors like congestion, port closures, labour strikes, extreme weather, or changes in fuel prices. The 2021 Suez Canal blockage delayed global trade by weeks, affecting $9 billion worth of goods daily. Another example is the shortage of truck drivers in Europe and North America, affecting the second-hand automobile market.
Multi-Modal Transportation
Using a mix of air, sea, rail, and trucking to ensure flexibility in case one mode is disrupted.
Route Optimization & Diversification
Working with logistics partners to identify alternative shipping routes and suppliers in different locations.
Technology & Real-Time Tracking
Using AI-driven logistics platforms for demand forecasting, real-time shipment tracking, and predictive analytics.
Strong 3PL Partnerships
Collaborating with third-party logistics providers (3PLs) with established contingency plans.
Inventory Buffering
Keeping safety stock in key locations to maintain supply during transit disruptions.
Regulatory & Compliance Risks
Suppliers may fail to meet quality standards, leading to defective products, recalls, or regulatory penalties. In 2013, food giant Nestlé faced scrutiny for using suppliers linked to forced labour, leading to reputational and legal challenges.
Mitigation Strategies:
Supplier audits and certifications
Require compliance with ethical sourcing and labour laws.
Automated compliance monitoring
Use software to track regulatory changes and ensure adherence.
Corporate social responsibility (CSR) programs
Invest in ethical sourcing and fair trade initiatives.
Inflation & Cost Volatility
Fluctuations in raw material prices, labour costs, and currency exchange rates affect supply chain costs. The main mitigation tactic here is locking in long-term contracts with fixed pricing.
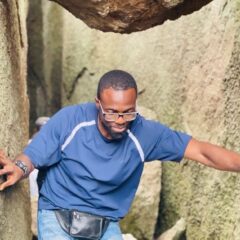
Olutobi
I write about business and project management.
10+ years working in program management. I've worked in health-tech, community health, regulatory affairs and quality assurance.